PID control
PID control is widely used in engineering for controlling industrial processes. In this post we will present the concept of PID control (proportional-integral-derivative controller) in a simplified way.
Objective
It is a process control technique that ensures that errors (disturbances) are minimized and corrected automatically.
How is it done?
The error is minimized by proportional action, zeroed by integral action and an anticipated speed is obtained by derivative action. For all this to work correctly, several mathematical calculations are made at an engineering level, which we do not want to go into in detail.
What do I need to know?
There are 3 values (P) = Kp, (I) = Ki and (D) = Kd, these 3 values are used in mathematical formulas.
P > Compared to the on-off action, it produces an output signal that is proportional to the error amplitude e(t).
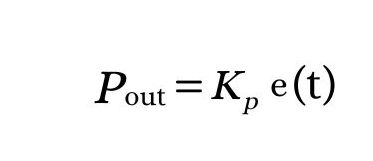
A proportional gain that is too high produces a high output signal, which can destabilize the system. However, if the proportional gain is too low, the system fails to take the necessary action to correct the system disturbances.
I > Integral action produces an output signal that is proportional to the magnitude and duration of the error.
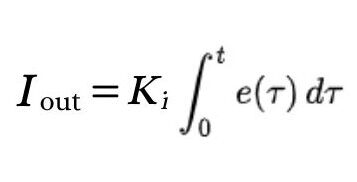
It makes it possible to correct the error generated by the proportional action (P) and accelerates the system response.
D > Derivative action produces an output signal that is proportional to the rate of variation of the error:
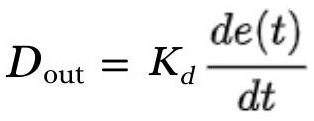
Note: Derivative action should not be used in processes in which the system must respond quickly to a disturbance, nor in processes that present a lot of noise in the measured signal, as this would lead to process instability. In practice, in many processes, (I) is set to zero.
Understand PID in practice
We have a resistor connected to the temperature controller, where the controller’s objective is to heat the resistor to the temperature programmed by the operator (Set-point). To obtain maximum efficiency, PID control is used, where the Set-point is reached in the shortest possible time.
It is important that the temperature remains stable after reaching the Set-point, even if there are deviations in the process (error), such as air jets, heat exchange with another material, change in the Set-point value. All this stability and efficiency is thanks to the PID control that recognizes (temperature sensor) the process deviations and immediately corrects the control at the output.
How to get PID values?
Different methods for tuning PID controllers are found in the literature, each method being indicated for a type of system. The most commonly used tuning methods in practice are:
- Ziegler-Nichol method without open loop.
- Ziegler-Nichol method without closed loop.
- Frequency response tuning.
- Root locus tuning.
IN SHORT, these are mathematical methods where a “step” input signal is applied, where time is measured until the application (output) reaches stability. The variation in the output creates a graphical design, where it is possible to extract values to start engineering mathematical calculations (integral / derivative / limit).
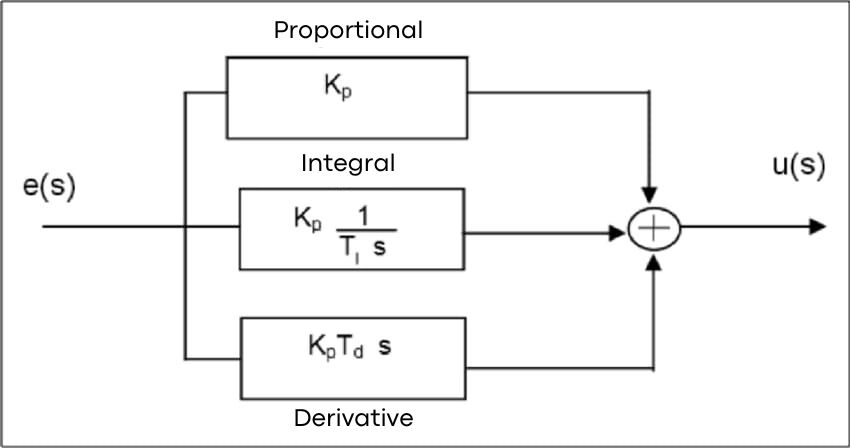
These mathematical methods are usually performed by manufacturers when developing equipment. When PID values are lost or there are physical changes in the application, we use the auto tuning method to obtain a new PID value.
How to perform Auto tuning?
Returning to our example of the temperature controller:
When activating the auto-tuning function on the controller, the Set-point is temporarily disregarded. This is because the controller will be turning the resistor on and off several times (repetitive testing).
Therefore, the temperature will go up and down in order to recognize the function:
Input (temperature) = Output (electrical power) x time.
The PID values are automatically defined at the end of the auto-tuning and the controller will once again respect the Set-point.
Conclusion
As seen in this post, the subject of PID control is not simple and should be observed carefully.
We conclude that when the process control is simple and does not involve many variables, auto tuning is sufficient. However, when it comes to complex processes or when there are physical changes in the equipment, the best option is to contact the manufacturer or perform all the mathematical calculations.
Legal Notice
All information obtained on this website and related social media pages is for INFORMATIONAL purposes only. The Way Automation is NOT responsible for any damage or loss caused by the execution of actions related or not to the content described here. Always look for a qualified professional, follow the rules and use protective equipment for any work that involves electricity.