PROFIBUS
In approximately 1940 instrumentation operated from 3 to 15 PSI (pneumatic signal) for the analog control system, the logics were carried out by mechanical contacts. With the evolution of technology
and the complexity of processes, this system was no longer viable. Thus appearing in the 1960s the sign from 4 to 20mA for analog control and discrete signals the programmable logic controller (PLC).
Timeline
In 1987 in Germany, 21 companies and institutes joined and created a strategic project in Fieldbus. The result was an open protocol where devices from different manufacturers communicate freely after being configured and added to the network. PROFIBUS is a field network pattern open and independent of suppliers, where the interface between them allows for wide application in processes, manufacturing and Automation. This standard is guaranteed in accordance with EN 50170 and EN 50254.
Since January 2000, PROFIBUS has been firmly established with IEC 61158, alongside seven more other Fieldbuses. Worldwide, users can now reference to an international standard of protocol, whose development sought and seeks cost reduction, flexibility, reliability, service the most diverse applications, interoperability and multiple suppliers.
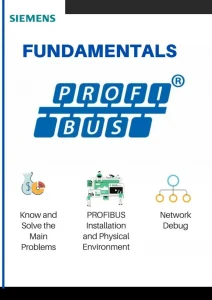
In this e-Book, we cover the good practices for installing Profibus DP/PA, main problems and solutions. Product intended for professionals in industrial automation, as well as technicians and engineers.
PROFIBUS FMS
The first step in 1989 was the specification of the PROFIBUS FMS communications (Specification of Fieldbus Messages), which has been prepared to requirement tasks communication. In 1993 was the completion of the specification for a simpler variant with faster communication, the PROFIBUS-DP. Based on these two communication protocols, coupled with the development of numerous application profiles oriented and a number of fast-growing devices, PROFIBUS began its progress initially in manufacturing automation and since 1995 in process automation with the introduction of PROFIBUS-PA. Today, PROFIBUS is the leading field bus on the world market.
Ethernet
The term Ethernet defines one of the protocols used in the TCP/IP architecture. Its origin was in the mid-1970s, created intel and xerox.
The great need for its use is due to the the need to link to supply chain levels (Supply Chain) involving a single and unique standard, TCP/IP. Thus, the level of management or sales would have access to the (sensor or actuator) in real time.
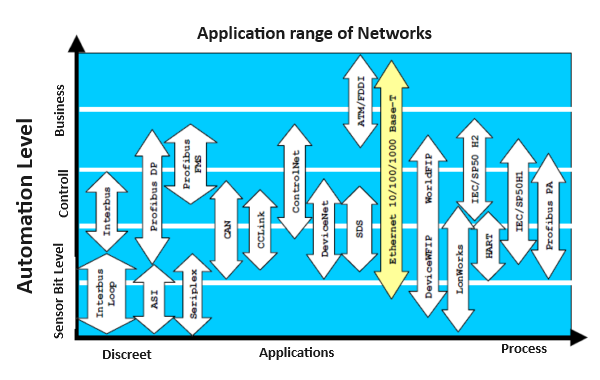
PROFINET
PROFINET is a network based on a standard of Industrial Ethernet communication standardized by IEC standards 61158-5 and IEC 61158-6, 100% technology compatible Ethernet (IEEE 802.3). Provides natural interaction with automation such as PROFIBUS, Interbu-S and others. The concept is integrate PROFIBUS segments into Ethernet and do not encapsulate the PROFIBUS protocol. For many years communication over the Ethernet network has been used in the industry between equipment as human interfaces machine (HMI), programmable logic controllers (PLC’s), SCADA systems, and also for programming, configuration and monitoring, however, there was no network based on Ethernet intended for the control of field devices.
PROFIBUS
PROFIBUS is a multi-master system and allows the operation of various automation systems, with their respective peripheral devices. PROFIBUS differentiates your devices between masters (PLC) and slaves (Actuators). Devices master determines the communication of data on the bus. A master can send messages whenever has the access right to the token. Masters are also active stations in the PROFIBUS protocol.
The slave devices are remote (periphery) devices, such as I/O modules, valves, speed drives variable and transducers. They have no right of access to the Token and can only send messages to the master or recognize incoming messages when requested. The slaves
are also called passive stations. PROFIBUS has had 3 extensions so far, being:
PROFIBUS (DP-V0), basic functions for DP and PA.
• Standard diagnosis.
• Configuration and parameterization.
• Exchange of basic cyclic data.
PROFIBUS (DP-V1), were created between 1990 and incorporated EN 50170 in 1998. It has resulted in considerable improvements in PROFIBUS PA.
• Acyclic reading and writing telegrams.
• Extended functions for parameterization and configuration.
PROFIBUS (DP-V2), are performance improvements in communication for high-speed system in servos, systems functional safety and drives.
• Standardized redundancy.
• Upload and download.
• Slave-to-slave communication (Publisher/Subscriber).
• Constant cycle time which reaches an accuracy of us.
Legal Notice
All information obtained on this website and related social media pages is for INFORMATIONAL purposes only. The Way Automation is NOT responsible for any damage or loss caused by the execution of actions related or not to the content described here. Always look for a qualified professional, follow the rules and use protective equipment for any work that involves electricity.